1. SAND BLAST
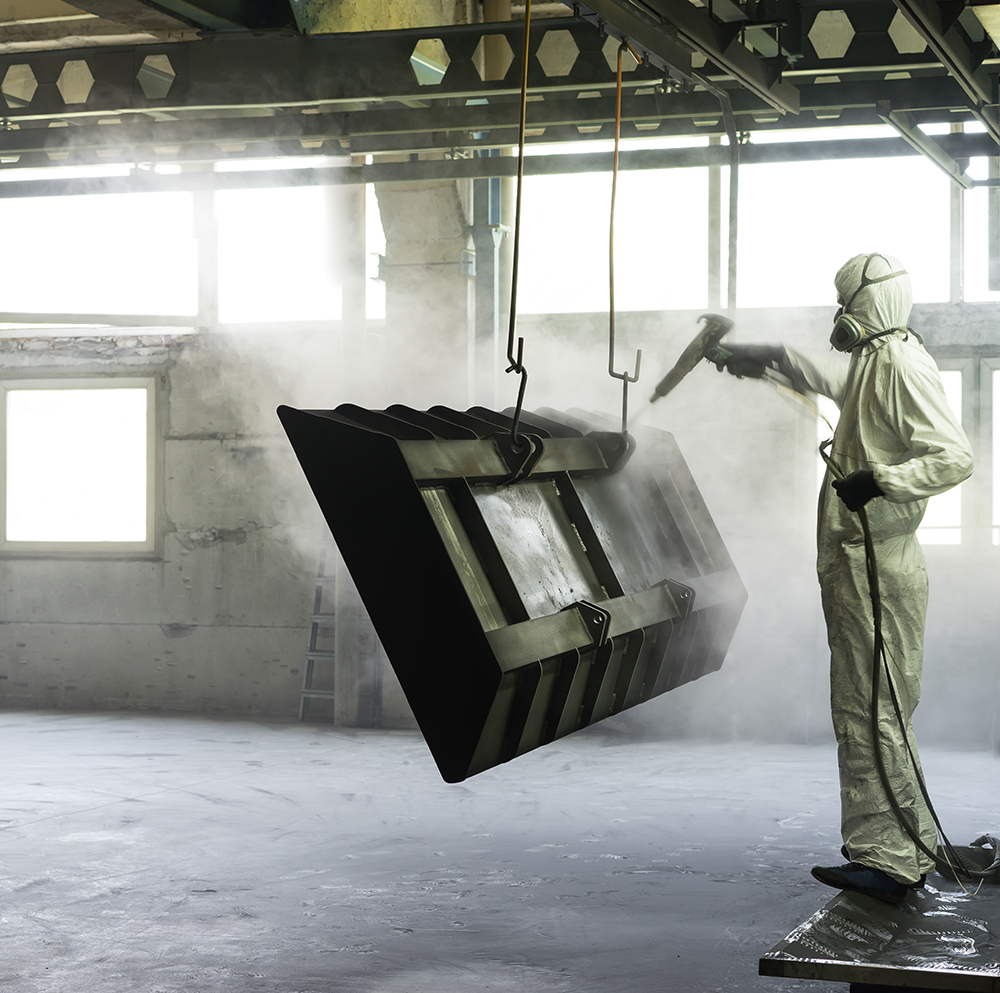
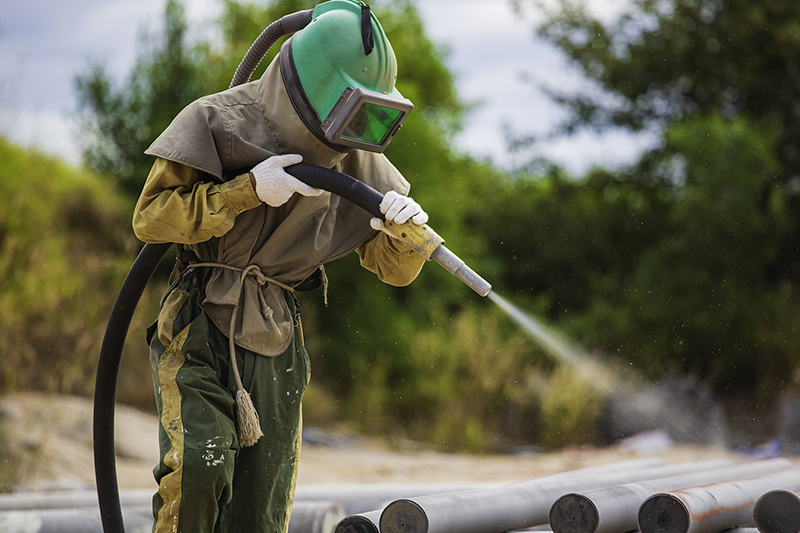
– It is the most important process before painting any product.
– To ensure the cleanliness of the product before painting it.
– The product is cleaned using materials known as Still Shot, which are iron granules of studied and specific sizes that enter a special machine to pump them using air pressure to contact the product and remove from it any deposits such as (carbon layer, oils, rust, and any other impurities that have stuck to the product).
Sandblasting, also known as abrasive blasting, is a surface preparation technique that involves the use of abrasive materials propelled at high speeds to clean, etch, or prepare a surface for various purposes. It is widely used in various industries and applications for its effectiveness in removing contaminants, rust, paint, and other unwanted materials from surfaces.
Applications: Sandblasting has a wide range of applications, including:
– Surface Preparation: It is commonly used to prepare surfaces for painting, coating, or bonding by removing rust, old paint, and contaminants.
– Cleaning: Sandblasting can clean surfaces that are heavily soiled, such as machinery parts, automotive components, and building exteriors.
– Etching: In artistic and decorative applications, sandblasting can be used to create intricate designs on glass, metal, or stone surfaces.
– Rust Removal: Sandblasting is effective at removing rust from metal surfaces, helping to extend the lifespan of equipment and structures.
3. PRODUCTION OF ZC GALVANIZED SECTIONS
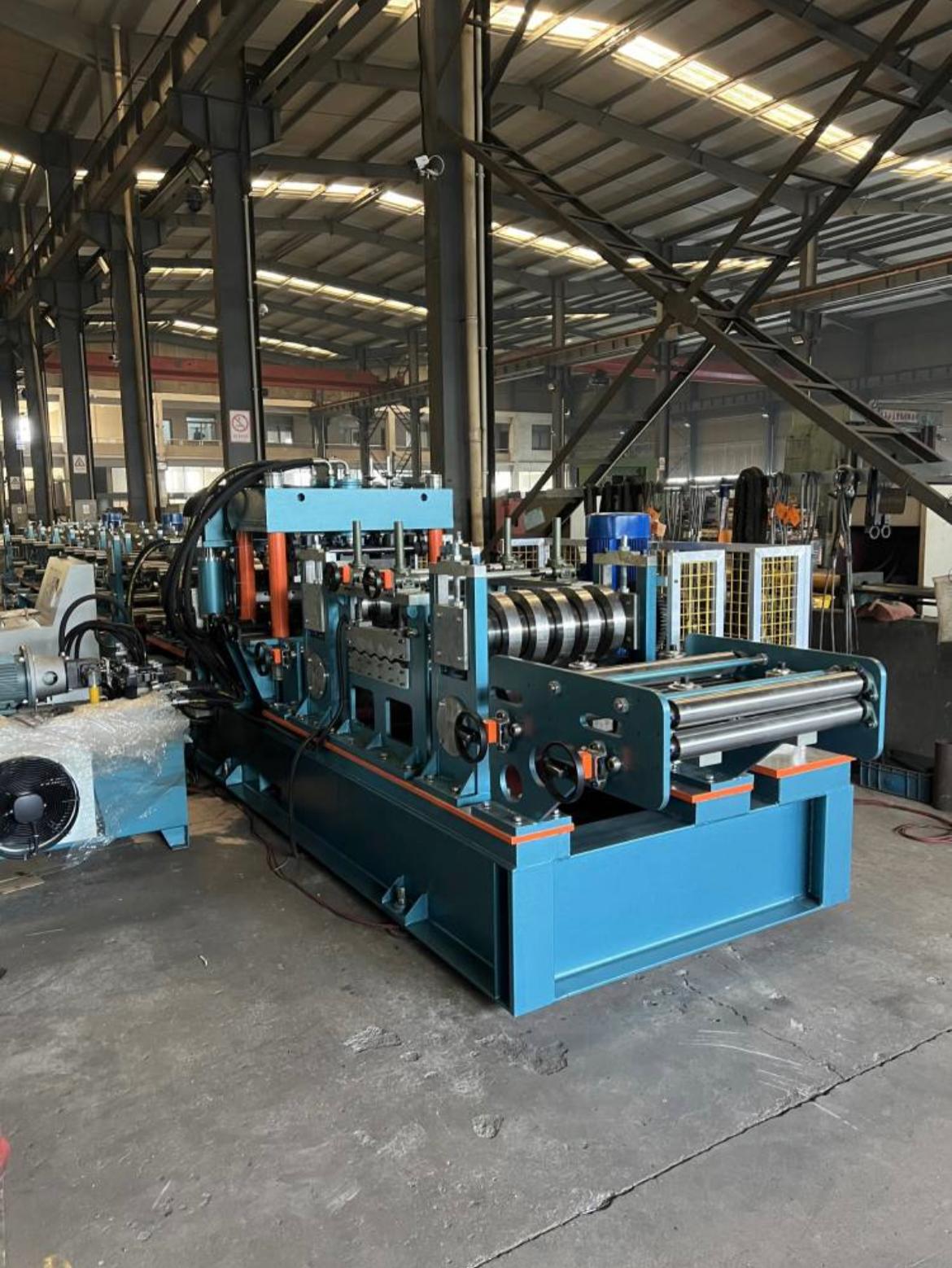
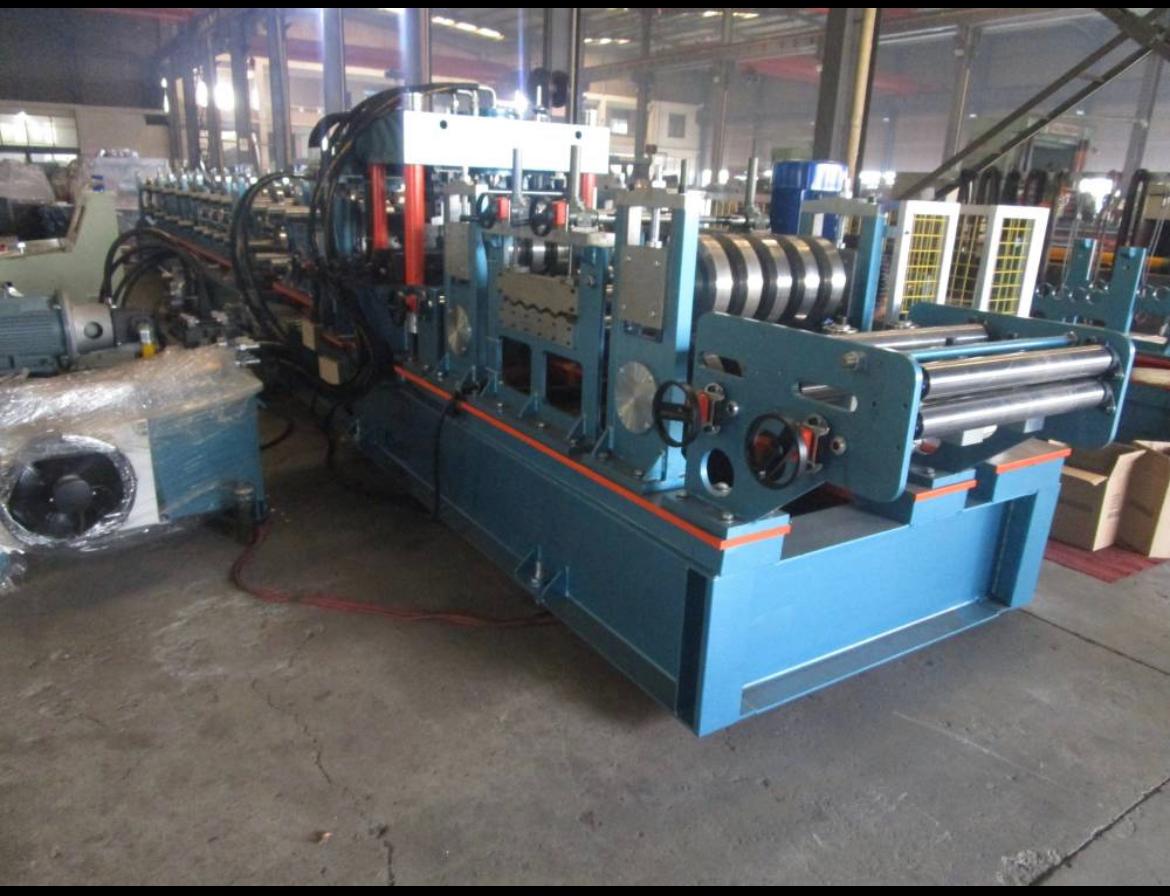
We produce this type of galvanized and black iron purlins using a machine with high specifications and very accuracy, and the dimensional differences do not exceed +/- 1-2 mm every 12 linear meters.
This product is widely used in steel buildings, and we can make any size ranging from 80 mm to 340 mm, with a hardness of 245/345/450 Newtons. Attached is a table of measurements.
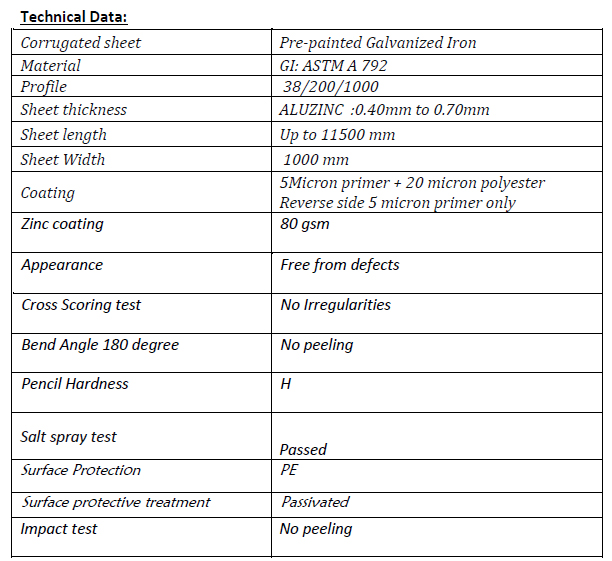
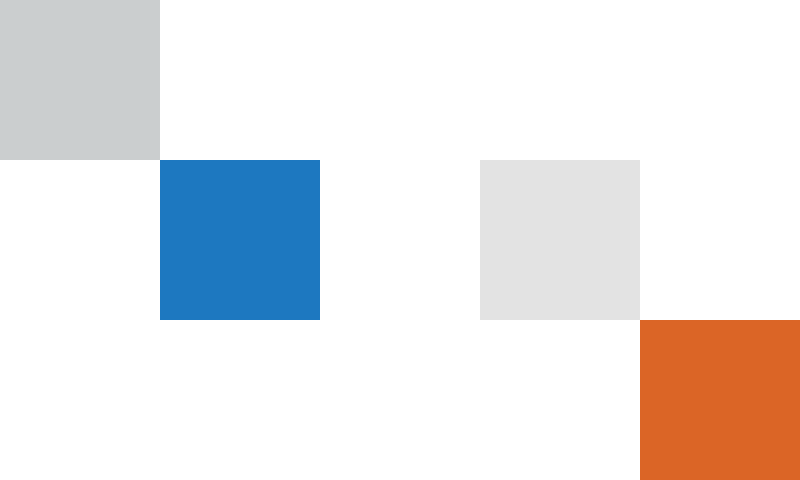
2. POWDER COAT
– The latest machines are used to paint metals and work using heat.
– This stage is considered one of the advanced stages in the field of thermal paint due to its high quality and the difficulty of causing changes in it, such as wounds and fractures, and its tolerance to natural factors, if it is done in the correct way.
As many stages must be performed before the painting process
Powder coating is a popular method of applying a durable and attractive finish to a wide range of materials, primarily metals but also some non-metallic surfaces. It involves the application of a fine powder made of pigments and resins onto a substrate, which is then heated to fuse the powder into a smooth and continuous coating. Here are the key aspects of powder coating:
Powder Material:
The powder used in powder coating is typically composed of finely ground particles of pigments, resins (usually thermosetting epoxy, polyester, or polyurethane), and sometimes additives such as flow agents and curing agents. The specific composition of the powder can be customized to achieve various finishes, textures, and performance characteristics.
Application:
The powder coating process involves electrostatic spray application or fluidized bed dipping. In the electrostatic spray method, the powder is electrostatically charged as it exits the spray gun, and this charged powder adheres to the grounded workpiece, creating an even and uniform coating. In fluidized bed dipping, the heated substrate is dipped into a fluidized bed of powder, and the powder adheres to the hot surface.
Curing: After the powder is applied to the substrate, the coated item is typically baked in an oven or heated with infrared lamps.
The heat causes the powder particles to melt and fuse together, forming a solid, continuous coating.
This curing process also enhances the coating’s adhesion and durability.
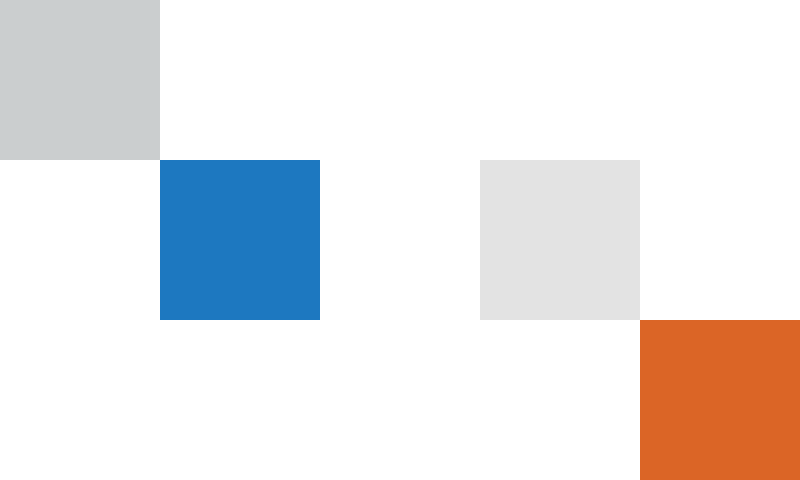
4. Ducking sheet
We produce this type of galvanized and black iron Ducking sheet using a machine with high specifications and very accuracy, and the dimensional differences do not exceed +/- 1-2 mm every 12 linear meters.
This product is widely used in steel buildings, and we can make size 900 mm width and 45 mm hight and space 241 mm , with a hardness of 245/345/450 Newtons. Attached is a table of measurements.
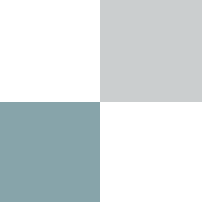
our mission is to craft and coat the future. We are dedicated to reshaping the landscape of metal construction and surface finishing with unwavering commitment to our core values
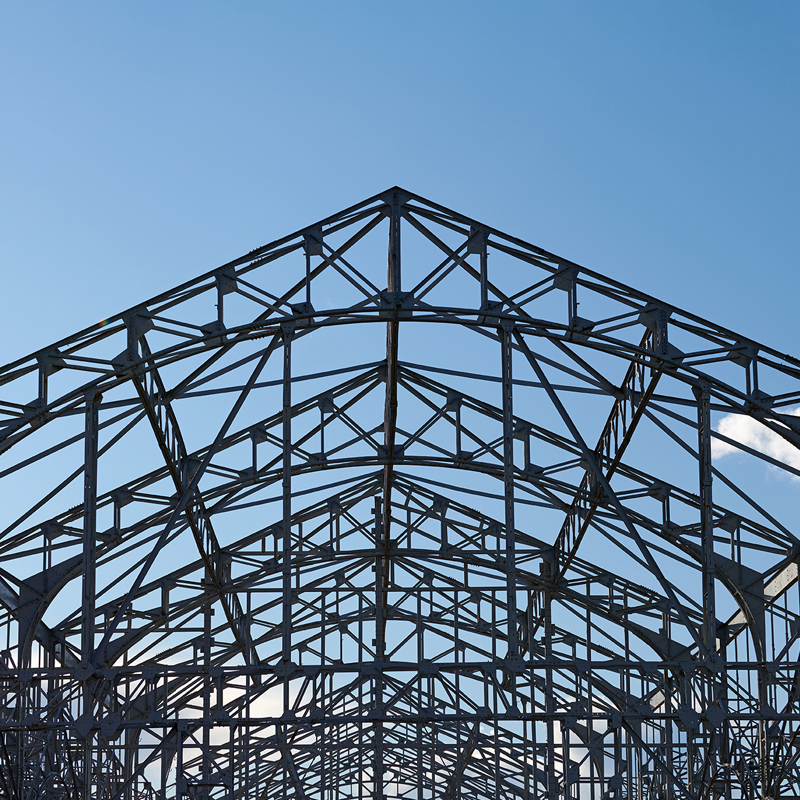
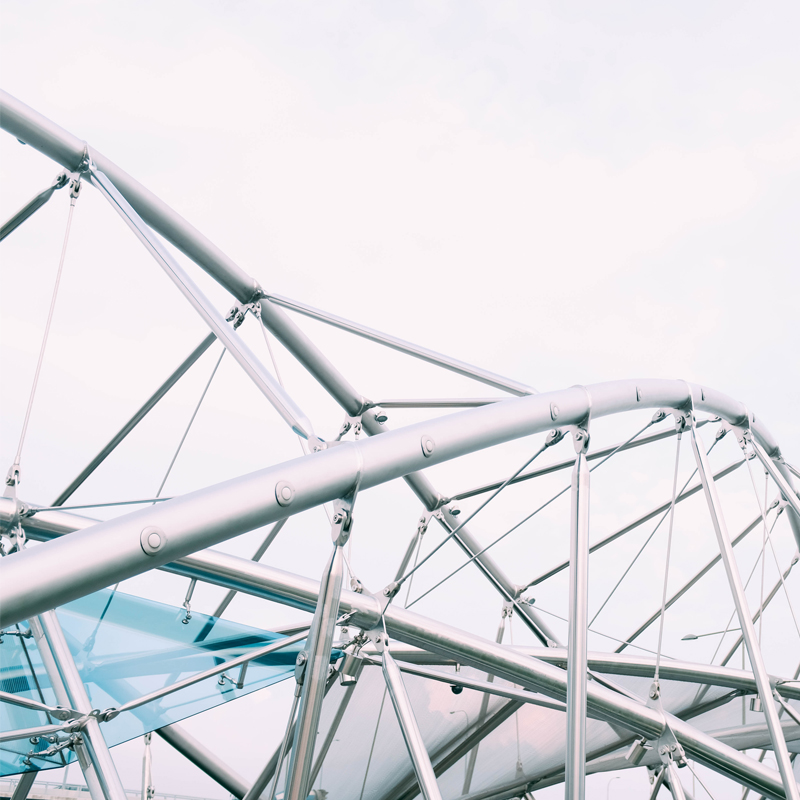
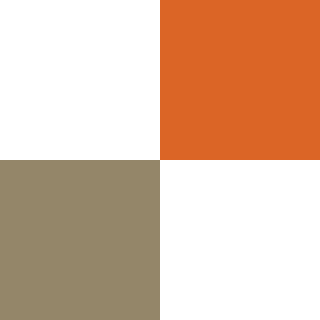
VALUES
The values and principles of our company revolve around
Contact us
(+974) 7703 0780 – (+974) 4475 9796
P.O.Box : 82440 Doha-Qatar
GM@tmc-qatar.com